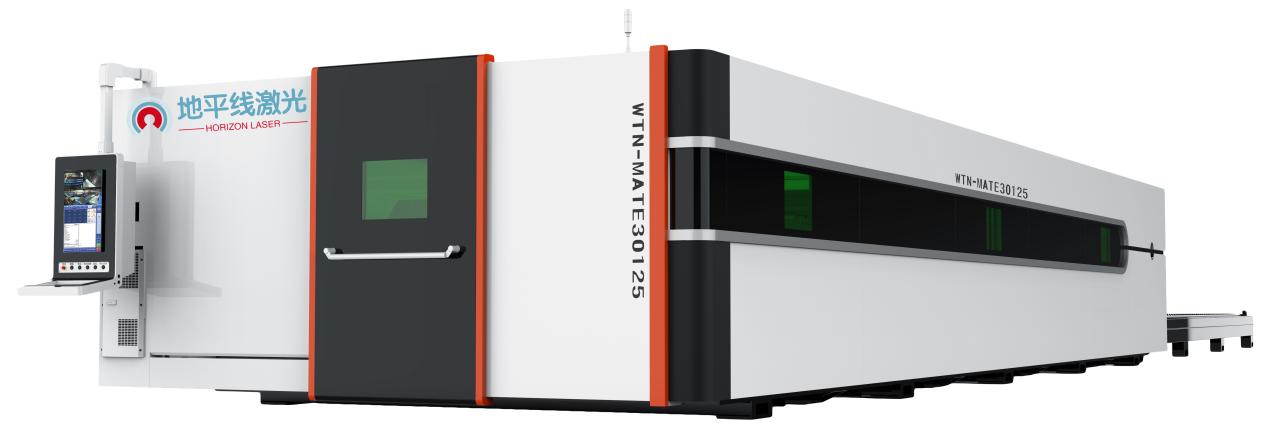
Note: Before debugging the cutting process, it is necessary to prepare the required cutting and debugging: nozzle, protective lens, plate, gas (N2, O2), clean workbench, microscope.
Materials |
Material Grade |
Stainless Steel |
SUS304 |
Carbon Steel |
Q235B |
1-Preparing for cutting
1.1 Optical path cleanliness inspection
Check steps:
Step 1: Make sure that the optical fiber and the cutting head are connected well, and the water cooling pipeline is running normally;
Step 2: Check the protective lens under the cutting head to ensure that the protective lens is clean;
Step 3: Turn on the laser, and use white paper to keep away from the nozzle of the cutting head (about 200~300mm away) to check the red light spot to ensure that the red light has no black spots and no abnormalities;
Step 4: If there is no abnormality in the above protective lens inspection and red light inspection, proceed to the next preparation link.
1.2 Adjust the laser to be in the center of the nozzle
Test Conditions:
Lighting method |
point light |
Nozzle |
1.2mm nozzle |
Test parameter |
Power: 1500W、Frequency: 5000Hz、Duty cycle: 50%、Shot time: 100ms |
Testing method:
Step 1: Adjust the focus position of the cutting head to the 0mm scale;
Step 2: Stick the scotch tape on the nozzle, point out the light, manually adjust the cutting head screw so that the laser point is in the center of the nozzle.
1.3 Laser focus position test
Test Conditions:
Lighting method |
point light |
Nozzle |
1.2mm nozzle |
Test parameter |
Power: 1500W、Frequency: 5000Hz、Duty cycle: 50%、Shot time: 100ms |
Testing method:
Step 1: Stick the textured paper on the nozzle;
The second step: every time the focal height changes by 0.5mm, the light is emitted;
Step 3: Compare the size of all points, find and record the corresponding position of the minimum point, which is the actual zero focus position, and the actual zero focus position is used as the benchmark for the subsequent cutting focus of different sheet thicknesses.
2-Cutting process debugging method
No. |
Debug Content |
Step |
First step |
Carbon steel cutting process debugging |
1. Ensure that the air pressure correction of the proportional valve is accurate;
2. Make sure that the plate is perforated or the edge of the plate starts to be cut; 3. Refer to the current power cutting machine process parameter table to find the cutting parameters corresponding to the thickness of carbon steel (laser power, gas type, air pressure, nozzle, cutting focus, cutting height); 4. Use the process parameter table to cut small squares. If the plate is cut continuously or the cutting section is not ideal, first adjust the cutting focus by 0.5mm up and down each time until the effect of cutting the plate or cutting section meets the requirements; 5. According to the effect, fix the cutting focus position under the optimal effect, and then adjust the air pressure up and down by 0.05bar each time to finally determine the cutting air pressure required for the optimal effect. Carbon steel cutting requires high oxygen pressure accuracy. (Carbon steel cutting requires high nozzle roundness and laser center point. After each nozzle replacement, it is necessary to reconfirm whether the laser is in the center of the nozzle) |
Second step |
Stainless steel cutting process debugging |
1. Ensure that the air pressure of the nitrogen gas cylinder is high enough (16-20bar). Insufficient air pressure will cause slow cutting speed, slag hanging on the cutting section, and layering of the cutting section;
2. Make sure that the plate is perforated or the edge of the plate starts to be cut; 3. Refer to the current power cutting machine process parameter table to find the cutting parameters corresponding to the stainless steel thickness (laser power, gas type, air pressure, nozzle, cutting focus, cutting height); 4. Use the process parameter table to cut small squares and use the lower limit of the cutting speed. If the cutting is continuous or the cutting section is not ideal, first adjust the cutting focus up and down by 0.5mm each time until the effect of cutting the sheet or cutting section meets the requirements; 5. According to the effect, fix the cutting focus position under the optimal effect, and appropriately increase the cutting speed, but cannot exceed the upper limit cutting speed, and take the stable batch cutting speed as the standard. |
Third step |
Aluminum alloy, copper high reflectivity material |
1. Aluminum alloy can be cut in small batches, but copper cannot be cut;
2. When cutting aluminum alloy, it is necessary to observe whether the plate is cut through. Once it is found that the plate is not cut through, stop immediately and reduce the cutting speed; 3. Do not cut aluminum alloy for a long time, it is recommended that each cutting time should not exceed half an hour 4. When cutting aluminum alloy, if the laser alarms, first check whether the laser has red light output. Each alarm should be stopped for 20 minutes, and the laser should not be restarted immediately for continuous cutting. |
3000W laser cutting machine cutting effect

Stainless steel:2-6mm
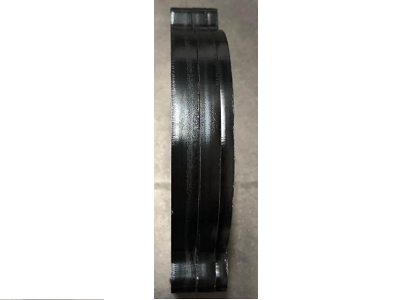
Carbon steel:4-8mm
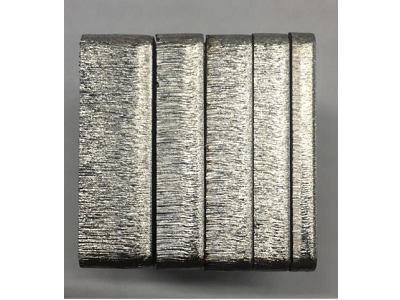
Stainless steel:4-10mm
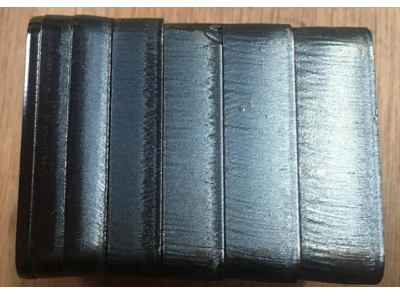
Carbon steel:4-16mm
Post time: Jul-19-2022